White Paper by on June 27, 2017
Download this white paper Meet the FormFoil® Family
Optimization of Cold-Form Foil Packaging
by Henk Blom, PhD
Introduction
Cold-form foils have been successfully deployed in pharmaceutical, medical device and in vitro diagnostic / point-of-care test kits for many years. As research scientists continue to create innovative solutions, demands on cold-form foils continue to grow and develop. It is critical, therefore, to have a solid understanding of the specific requirements that these foils need to meet, how the desired performance is realized, and how both requirements and material design impact the overall package design. In this white paper, we will look more closely at the interaction of cold-form foil requirements, package design, and manufacturing processes, with a view to understanding how all of these need to work together to achieve optimal package performance so that patients can receive the life-saving therapies they need.
Cold-Form Foil Requirements
In the early 1960’s Karl Klein developed the first machine¹ to form materials comprising aluminum foil into cavities or blisters that could hold a solid drug. Since that time, this technology has been implemented in a variety of other applications, most notably in medical device and point-of-care test kits. In its simplest form, the cold-forming process transforms a flat flexible barrier material containing a layer of aluminum foil into shapes such as shown in Figure 1. Normally, this shaping process occurs at ambient temperatures (in contrast to thermoforming, which requires heat) and involves a form and plug into which the material is pressed.
Cold-form foil materials serve a number of very important purposes in the packaging of items such as drug capsules, sutures, and diagnostic fluids. While each specific application will have its own unique requirements, in nearly every case requirements such as oxygen and moisture barrier, physical product protection during manufacturing, distribution and use, sealability to a lid or other device component, and ease of manufacturability factor into the package design process. Other requirements that often arise involve opacity (to safeguard against UV exposure), chemical resistance, appearance, and ease of opening, to name a few. It is important to understand all the nuances of a particular product to make certain that your package is optimally designed for market success.
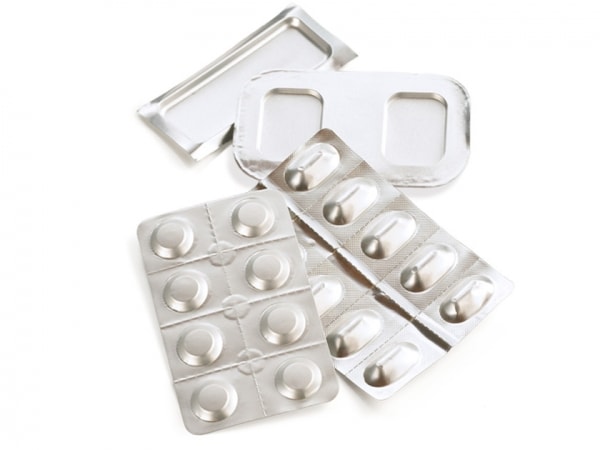
Figure 1 – Common cold-form foil shapes
Material, Process, and Design Considerations
The shaping of the flexible barrier material during the cold- forming process causes local stretching (and
consequent thinning) of the film. The degree of thinning is strongly dependent on the depth of the form,
the cross-sectional area (or footprint) of the form, and the draft angle at which the film is formed. The
draw ratio, a value commonly used in cold-forming design discussions, is the quotient of final surface
area after drawing (Af) over the starting cross- sectional area (Ai)….
Download this resource as a PDF to access the complete white paper